|
|
The Second International Workshop on Origami Engineering will be held from 6 to 8 November, 2017, in Tianjin University, Tianjin, China, following the first one in UIUC organised by Professor Glaucio Paulino back in 2014.
The objective of the workshop is to bring together researchers from all aspects of origami to exchange ideas and share views about the cutting-edge topics in the area, and to promote the applications of origami in science and engineering. The workshop will consist of keynote sessions from world leading experts and poster sessions for domestic and international researchers to present their research outcomes. Top 10% of the posters will be selected for the Best Poster Award.
|
|
Glaucio H Paulino
|
|
Origami Engineering: from Deployable Structures to Configurational Metamaterials |
|
We explore origami stiffness properties and, in particular, we study how geometry affects origami behavior and characteristics. Understanding origami from a structural standpoint can allow for conceptualizing and designing feasible applications across scales and disciplines of engineering. We review the basic mathematical rules of origami and use 3D-printed origami legos to illustrate those concepts. We then present an improved bar-and-hinge model to analyze the elastic stiffness, and estimate deformed shapes of origami – the model simulates three distinct behaviors: stretching and shearing of thin sheet panels; bending of flat panels; and bending along prescribed fold lines. We explore the stiffness of tubular origami and kirigami structures based on the Miura-ori folding pattern. A unique orientation for zipper coupling of rigidly foldable origami tubes substantially increases stiffness in higher order modes and permits only one flexible motion through which the structure can deploy. Deployment is permitted by localized bending along folds lines; however, other deformations are over-constrained (and engage the origami sheets in tension and compression). Furthermore, we couple compatible origami tubes into a variety of cellular assemblages including configurational metamaterials. We introduce origami tubes with polygonal cross-sections that can reconfigure into numerous geometries. The tubular structures satisfy the mathematical definitions for flat and rigid foldability, meaning that they can fully unfold from a flattened state with deformations occurring only at the fold lines. From a global viewpoint, the tubes do not need to be straight, and can be constructed to follow a non-linear curved line when deployed. From a local viewpoint, their cross-sections and kinematics can be reprogrammed by changing the direction of folding at some folds. The presentation concludes with a vision toward the field of origami engineering, including multifunctional origami, e.g. reconfigurable origami antennas. |
|
About Glaucio H Paulino |
|
 |
|
Professor Paulino is the Raymond Allen Jones Chair at the Georgia Institute of Technology. Prior to joining Georgia Tech in January 2015, he was the Donald and Elizabeth Willett Professor of Engineering at the University of Illinois at Urbana-Champaign (UIUC). His seminal contributions in the area of computational mechanics include the development of methodologies to characterize the deformation and fracture behavior of existing and emerging materials and structural systems; topology optimization for large-scale multiscale/multiphysics problems; and deployable structures and origami engineering; the latter being the topic of his lecture. He received the Walter L. Huber Civil Engineering Research Prize from ASCE (2004) and he is a fellow of USACM (2011), IACM (2012), and AAM (2015), and ASCE/EMI (2017). He received the 2014 Ted Belytschko Applied Mechanics Award from ASME; and the 2015 Cozzarelli Prize from the National Academy of Sciences, “which recognizes recently published PNAS papers of outstanding scientific excellence and originality.” He was the Shimizu Professor at Stanford Univ. in 2016 and the 2017 Southwest Mechanics Lecture Series Speaker. He is associate editor of the Journal of Optimization Theory & Applications, ASCE J. of Eng. Mechanics, and Mechanics Research Communications, and a regional editor of the International Journal of Fracture. His contributions to the permanent scientific literature include more than 200 scholarly publications in peer-refereed international journals, and a book on The Symmetric Galerkin Boundary Element Method (Springer-Verlag, 2008). He is presently vice-President of the Society of Eng. Science (SES) and a member of the Board of Directors of EMI (Engineering Mechanics Institute). |
|
|
Zhong You
|
|
Origami Mechanical Metamaterials with Programmable Stiffness |
|
Past research has shown that the formation of origami structures and the shape change capability of some origami objects can be readily parameterised and applied to the development of new metamaterials. In this talk, I shall focus on two types of origami structures constructed by interlinked and purposely designed origami units. The first is family of honeycomb structures derived from tessellation origami patterns, and the other is a set of block structures inspired by modular origami concepts. Both structures contain a motion phase where the units simply rotate about creases, and a structural deformation phase when the motion terminates and all of the structural units are packed together. Both structures can be tuned to acquire a programmable stiffness. The programmability is achieved by utilising different units in the large assembly. Using these two set of examples, I shall show that not only can the origami technique be effectively exploited to develop novel foldable structures, but it can also be used to induce particular structural deformation modes that lead to variable mechanical properties. I hope that the talk could stoke some common interests in this young but thriving area of research, and I am looking forward to possible collaborations on one or all of the topics introduced in this talk and beyond. |
|
About Zhong You |
|
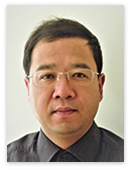 |
|
Dr Zhong You is a professor of engineering science at University of Oxford. His specific area of research is deployable structures, which include origami structures, structures with multiple stability, energy absorption structures, structural assembly of mechanisms, and structures for minimum invasive surgery (e.g., flow diversion stent for treatment of cerebral aneurysms and surgical devices for brain surgery). He has published widely in prestigious journals such as “Science”, and his research outcome has been selected to exhibit in the Royal Society’s Science Day Exhibition at the Buckingham Palace. “Science” introduced his research on origami engineering in the profile section. |
|
|
Larry Howell
|
|
Modeling, Design, and Application of Origami-Based Engineering Systems How Origami-Based Engineering can Impact our World |
|
Origami artists’ methods and perspectives have created systems that have not previously been conceived using traditional engineering methods. Using origami-inspired methods, it may be possible to design origami-like systems, but using different materials and processes to meet emerging product requirements. This presentation will highlight research in origami-based engineering at Brigham Young University, and will include a diverse set of applications. |
|
About Larry Howell |
|
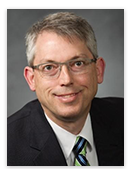 |
|
Larry L Howell is an Associate Dean and Professor at Brigham Young University (BYU). Prof. Howell received his B.S. degree from BYU and M.S. and Ph.D. degrees from Purdue University. Prior to joining BYU in 1994 he was a visiting professor at Purdue University, a finite element analysis consultant for Engineering Methods, Inc., and an engineer on the design of the YF-22 (the prototype for the U.S. Air Force F-22 Raptor). He is a Fellow of ASME, past chair of the ASME Mechanisms & Robotics Committee, and has been associate editor for the Journal of Mechanisms & Robotics and the Journal of Mechanical Design. He is the recipient of the ASME Machine Design Award, ASME Mechanisms & Robotics Award, Theodore von Kármán Fellowship, NSF Career Award, Purdue Outstanding Mechanical Engineer (alumni award), and the BYU Karl G. Maeser Distinguished Lecturer Award (BYU’s highest faculty award). Prof. Howell’s research focuses on compliant mechanisms, including origami-inspired mechanisms, space mechanisms, microelectromechanical systems, and medical devices. He is the co-editor of the Handbook of Compliant Mechanisms and the author of Compliant Mechanisms which are published in both English and Chinese. His lab’s work has also been reported in popular venues such as Newsweek, Scientific American, Popular Science, and the PBS documentary program NOVA. |
|
|
Mark Bolitho
|
|
Creative Origami Methodologies: an Approach to Origami Design |
|
An exploration of how origami designs are made and developed, based on my experience in developing models for clients and developing applied folding in product design. As a designer there is a point where a folded project is complete and the model is considered to be complete and “finished”. However, from time to time improvements can be made or are realised, which may enhance or develop an idea. In my talk I will look at my design process and identify when this has happened. Also I will look at other design methodologies and a group approach to optimising Origami design. |
|
About Mark Bolitho |
|
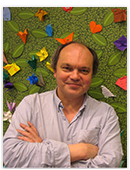 |
|
Mark Bolitho is a world renowned origami artist. In 2004 he decided to change his career from being an accountant to working full time on paper folding projects. Based in the United Kingdom he now works full time as an origami designer.
He has worked with a variety of clients to produce bespoke origami designs to meet commercial and artistic briefs. Clients include advertising and design companies, event companies, publishers and academic institutions. Projects have included television and print advertisements, websites, newspaper articles and direct marketing campaigns.
Mark has worked as an origami demonstrator throughout the world in countries including France, Germany, Switzerland, Japan, Korea, and Dubai. In 2008 he was selected as one of 50 guest speakers at IdeaCity in Toronto, Canada. In 2009 he was honoured to be a special guest at the annual Nippon Origami Association (NOA) Symposium in Japan. He is a long standing member of the British Origami Society and has previously been the Chairman of the Society.
He is the author of several books on instructional origami including Origami Home (2014) and more recently The Perfectly Mindful origami series Garden (2017) and Geometric shapes (2017) and Dr Who Origami (2017). He is one of the co-organisers of 7OSME that will take place in 2018..uk |
|
|
Kyu-Jin Cho
|
|
Origami Wheel Transformer:
a Variable-Diameter Wheel Drive Robot Using an Origami Structure |
|
A wheel drive mechanism is simple, stable, and efficient, but its mobility in unstructured terrain is seriously limited. Using a deformable wheel is one of the ways to increase the mobility of a wheel drive robot. By changing the radius of its wheels, the robot becomes able to pass over not only high steps but also narrow gaps. We propose a novel design for a variable-diameter wheel using an origami-based soft robotics design approach. By simply folding a patterned sheet into a wheel shape, a variable-diameter wheel was built without requiring lots of mechanical parts and a complex assembly process. The wheel’s diameter can double with the transformation, and it is light in weight. Although composed of soft materials (fabrics and films), the wheel can bear more than 400 times its weight. |
|
About Kyu-Jin Cho |
|
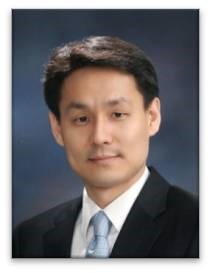 |
|
Kyu-Jin Cho received B.S and M.S. degrees from Seoul National University, Seoul, Korea and a Ph.D. degree in mechanical engineering from Massachusetts Institute of Technology. He was a post-doctoral fellow at Harvard Microrobotics Laboratory. At present, he is an associate professor of Mechanical and Aerospace Engineering, the director of Soft Robotics Research Center and the director of Biorobotics Laboratory at Seoul National University. His research interests include biologically inspired robotics, soft robotics, soft wearable devices, novel mechanisms using smart structures, and rehabilitation and assistive robotics. He has been exploring novel soft bio-inspired robot designs, including a water jumping robot, flytrap inspired robot and a soft wearable robot for the hand, called Exo-Glove. The work on the water jumping robot was published in SCIENCE and covered by over 300 news media world-wide. He has received the 2014 IEEE RAS Early Academic Career Award for his fundamental contributions to soft robotics and biologically inspired robot design. He has also received the 2014 ASME Compliant Mechanism Award, 2013 IROS Best Video Award, 2015 KROS Hakbo ART (Assistive Robotic Technology) Award and 2013 KSPE Paik Am Award. The Biorobotics Lab has won the 1st RoboSoft Grand Challenge (April, 2016) sponsored by European Commission with the robot “SNUMAX” in Livorno, Italy. |
|
|
Wenwu Chang
|
|
Geometry behind Flat-fold Cone and Honeycomb |
|
In this lecture, I will mainly discuss two topics: one is the twist fold of a cone ; Another is the space-filling cube origami.
During the first part of discussion I will talk about the background of the topic which is triggered by a series of dresses designed by Issey Miyake's team. then by mathematics analysis a formula is established to ensure the original cone be folded flat completely. Actually this is a sufficient and necessary condition to do so. In the end of this topic, an application in paper cup manufacturing will be shown to the audience.
In the second phase of my lecture, I will explain how to fold a basic module of cube frame from a rectangle sheet. The rectangle sheet will need to first covered by a net of of parallel creases whose slope be ±sqrt(2). That is the slope of a diagonal on a A4 paper. Finally, a theory of so-called cut-melt scheme will be given to extend the cube to infinite honeycomb structure. That means given a sufficient large paper, one can always origami as many cubes as he wants from it and the paper would keep a whole sheet without cutting. This result may not be just of mathematical meaning, it will benefit the package industry by saving plastic foam as filling material. |
|
About Wenwu Chang |
|
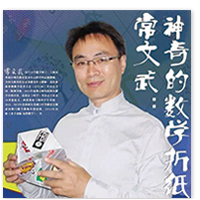 |
|
Wenwu Chang is an interdisciplinary senior teacher at modern educational technology center in Shanghai. He obtained his Ph.D. in mathematics from Fudan University, China. |
|
|
Ichiro Hagiwara
|
|
Current State and Issues of Industrialization from Origami-engineering |
|
It has passed around 15 years since Dr. Nojima proposed Origami-engineering on November, 2002. Till now, Origami structure has been used in aerospace structures because in aerospace it can be permitted even in high cost manufacturing. In another industries, it is not permitted in high-cost manufacturing even though origami structure has excellent characteristics such as foldable & deployable and light & stiff. For example, most of vehicle crash energy-absorbed structures are developed by author's patent. Even now, it has 2 weak points such as initial peak load is high and only 70% collapsed in its length. We have shown Reversed Spiral Origami Structure (RSO) can solve these items and optimized RSO can absorb crash-energy 1.4 times of present vehicle crash-energy absorbing structure. But among present manufacturing methods, only hydroforming method is applicable for RSO of steel. And the manufacturing cost is too high to be applied in real structure. Here we show the new and very cheap manufacturing method named partial revolution torsion method (PRT). Based on PRT method, we have developed new excellent structure named Reversed Torsion Origami Structure (RTO). Here we show RTO is more excellent than RSO, of course, much more excellent conventional crash absorbing structure. In such way, except crash energy-absorbing structure, gradually there have been industrialized some items such as isolators, the lightest safety foldable helmet, assembly Truss Core panel (ATCP) etc.. And we have developed Origami printer which is superior to 3D Additive printer in some points because 3D Additive printer is corresponding to forging and casting, not corresponding to pressamong 3 type manufacturing styles. It is the 3D Origami printer which corresponds to press. From now on Origami folding robot and Origami printer are the key technologies for more industrialization from Origami engineering. |
|
About Ichiro Hagiwara |
|
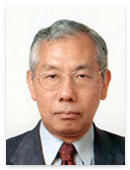 |
|
Professor of MIMS(Meiji Institute for Advanced Study of Mathematical Sciences),
Emeritus Professor of TIT(Tokyo Institute of Technology) |
|
|
Guoxing Lu
|
|
Impact Response of Graded Cellular Materials and Origami Metamaterials |
|
In this presentation, I will first report, in detail, our studies of graded (non-uniform) cellular materials subject to impact loading. The cellular material could have gradient in plateau stress, relative density and locking strain. A double-shock analytical model has been proposed where two plastic shock waves propagate towards each other, rather than only one shocfront as in the case of a uniform cellular material. Finite element analysis was also performed. Most recently, experiments were conducted with a simplified graded cellular material, where plastic deformation was captured by using high-speed photography and impact force was measured by using a Hopkinson bar. The impact force, force at the support (distal end) and the energy absorption of the graded cellular material are investigated thoroughly. Depending on applications, the graded cellular material should be arranged accordingly in order to achieve an optimum outcome.
From the viewpoint of impact mechanics, graded origami metamaterial bears a strong similarity to graded cellular materials. Hence, in the second part I will highlight some key parameters and outline possible approaches to studying the impact response of graded origami metamaterials. Some preliminary results will be presented. |
|
About Guoxing Lu |
|
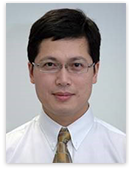 |
|
Guoxing Lu is Professor in Impact Engineering and Chair, Department of Mechanical and Product Design Engineering, Swinburne University of Technology, Melbourne, Australia. He obtained his PhD in Structural Mechanics from the University of Cambridge in 1989, supervised by Professor CR Calladine, FRS, FREng. Professor Lu has over 30 years of research experience in the field of impact engineering. He was a tenured faculty member at Nanyang Technological University, Singapore before he returned to Swinburne in 2015. His research interest is in energy absorption, dynamic behaviour of engineering materials at high strain-rates, structural response to impact, blast and shock loads and structural protection. He has published over 190 papers in international journals. His total number of citations is 4500 with an H-index 35. He has written a monograph with Professor TongXi Yu entitled “Energy Absorption of Structures and Materials”, 2003.
Professor Lu is an Associate Editor of International Journal of Impact Engineering and a member of editorial board of four other international journals. He is a founding Board Member of the International Society of Impact Engineering. |
|
|
Marc Miskin
|
|
From Atomic Origami To Cell-Sized Machines |
|
Origami presents an attractive platform for miniaturizing machines: thinner layers of folding material lead to smaller devices. Here, we take origami fabrication to its ultimate limit by using 2D atomic membranes as the folding materials. Working with graphene, glass, platinum, and DNA, we bond layers of these materials together to make atoms thick bimorph actuators that bend to micron radii of curvature. By patterning rigid panels on top of these actuators, we can localize bending to produce folds and scale down existing origami patterns to produce a wide range of machines. These machines change shape in fractions of a second in response to environmental changes, and perform useful functions on time and length scales comparable to microscale biological organisms. Beyond simple folding, this technology presents direct routes to integrate with silicon based electronics, enabling a powerful platform for robotics at the cellular scale. |
|
About Marc Miskin |
|
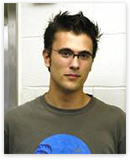 |
|
Marc Miskin is a Kavli Institute Postdoctoral Fellow in Nanoscale Science at Cornell. His work centers on building cell sized structures and machines by folding atomically thin sheets of paper. He has been at Cornell since receiving his PhD in physics from the University of Chicago in 2014. His work has won several awards including a Springer Thesis Award and the Grainger Fellowship for excellence in experimental physics. Outside of research, he is actively involved in public science education, frequently appearing
as a presenter at the local children’s science museum. |
|
|
Yves Klett
|
|
Overview of Mechanical Properties of Foldcore-based Sandwich Structures |
|
Folded structures in the form of tessellations have by now been established as alternative sandwich core material for high-performance lightweight applications. Several studies on the potential of Miura-ori and related tessellations have been presented in the last few years by different research groups. Due to the large number of possible combinations of materials and geometries, generation of a coherent picture of the overall performance of foldcores can be quite challenging.
We will present a compilation of the results of number of parametric studies carried out at the Institute of Aircraft Design (University of Stuttgart), which use a common methodology to evaluate mechanical properties of different unit cell geometries, with a focus of generating comparable results.
Data on the mechanical properties especially includes shear strength and stiffness. While favorable shear properties of foldcores have already been predicted by very early studies, useful data on shear properties has been sparse. We present the results of a number studies using both experimental as well as simulation setups. Experimental data has been collected for foldcores made from aramid-paper composites and thermoplastics, and has been supplemented by finite element analysis with a focus on isotropic materials. On the simulation side, a method to efficiently represent foldcore geometries and to realistically represent manufacturing imperfections has been developed anew.
The presented results add to the already existing data corpus, and give new insights on the influence of unit cell geometry on the compressive and shear performance of foldcore tessellations, and shed new light on interesting aspects like shear anisotropy and overall potential of folded structures for sandwich core applications. |
|
About Yves Klett |
|
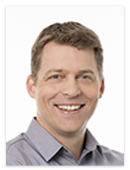 |
|
Yves Klett studied aerospace engineering in Stuttgart, Germany, where he fell for the charms of origami in the form of folded high-performance structures. Since getting a PhD in advanced paper folding, he is leading the sandwich technology group at the Institute of Aircraft Design in Stuttgart, which specializes in the design and industrial manufacture of origami-based foldcores for technical applications. |
|
|
Yan Chen
|
|
Rigid Origami |
|
To solve the rigidity of origami patterns, a kinematic model has been set up. Firstly, we can use this model to judge the rigidity of origami pattern; secondly, with the reverse kinematics, the rigid origami patterns can be designed directly; thirdly, the parameter study on the pattern geometry leads to more varieties and graded patterns. It is interesting to find that for the same pattern, the mountain-valley fold assignment takes a great role in its rigidity. Therefore the deformation of the corresponding metamaterials. In addition, a simple switch of mountain-valley assignment on existing patterns can enable discovery of new metamaterials potentially with more intriguing properties such as 3D negative Poisson's ratio or programmable stiffness. This work will not only clear the arguments on origami foldability and rigidity, but also open up a new arena for the design of origami-inspired metamaterials with a broadened range of properties.
With our previous result on the thick-panel origami, a transition technique has been proposed by taking the thick-panel form of an origami pattern as an intermediate bridge. A zero-thickness rigid origami pattern and its thick-panel form share the same sector angles and folding behaviours, while the thick-panel origami and the mobile assembly of linkages are kinematically equivalent with difference only in link profiles. Applying this transition technique to typical four-crease origami patterns, we have found that the Miura-ori and graded Miura-ori patterns lead to assemblies of Bennett linkages with identical link lengths. The supplementary type origami patterns with different mountain-valley crease assignments correspond to different types of Bennett linkage assemblies with negative link lengths. And the identical linkage type origami pattern generates a new mobile assembly. Hence, the transition technique offers a novel approach to construct mobile assemblies of spatial linkages from origami patterns. |
|
About Yan Chen |
|
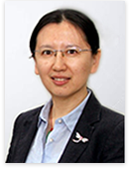 |
|
Professor Yan Chen, PhD (Oxford, UK), CEng, FIMechE
Dr. Yan Chen is a professor in School of Mechanical Engineering at Tianjin University, China. She received her PhD in structural engineering at University of Oxford, UK in 2004. With a short PostDoc research experience in Oxford, she became an assistant professor in School of Mechanical and Aerospace Engineering at Nanyang Technological University, Singapore. In 2012, she moved to Tianjin University as a professor. She is also the Fellow of Institution of Mechanical Engineers UK and the Vice-Chair of Chinese Committee, International Federation for the Promotion of Mechanism and Machine Science (IFToMM).
Her research specialty is on the emerging and advanced structures, which have internal mobility for shape transformation, with kinematics and mechanics as the theoretical foundations, aerospace deployable structures and robotics as application platforms, light-weight eco-material and medical microstructures as extension. Recently, she has applied the advanced kinematic theory to analysis and synthesis of rigid origami patterns. In 2015, her team has solved the problem on origami of thick panels, one of the major challenges in origami engineering, which was published on Science. |
|
|
|
|
Time |
Monday |
Tuesday |
Wednesday |
Hongyuan Lecture Theater |
8:10am-8:30am |
Welcome speech and group photo |
Lab tour and poster session |
Lab visit and discussion |
8:30am-9:30am |
Glaucio H Paulino | Ichiro Hagiwara |
9:30am-10:30am |
Zhong You |
Mark Bolitho |
10:30am-11:00am |
Coffee break and
poster session |
Coffee break and
poster session |
11:00am-12:00pm |
Larry Howell |
Guoxing Lu |
12:00pm-1:30pm |
Lunch |
Lunch |
1:30pm-2:30pm |
Wenwu Chang |
Marc Miskin |
2:30pm-3:30pm |
Kyu-Jin Cho |
Yves Klett |
3:30pm-4:00pm |
Coffee break |
Coffee break and
poster session |
4:00pm-5:00pm |
Lab tour |
Yan Chen |
5:00pm-6:00pm |
Award ceremony,
workshop closure |
|
|
|
|
|
The workshop will be held on the new Peiyang Park Campus of Tianjin University, 135 Yaguan Road, Jinnan District, Tianjin, 300354, China. Tianjin is a city 150 km south east of Beijing. Accommodations for invited speakers will be provided at the nearby Crystal Palace Hotel located on 28 Youyi Road (Youyi Lu), Hexi District, Tianjin, 300061, China. Please contact workshop organizers with arrival and departure times to make travel arrangements. The organizers can also help domestic participants to book accommodations at Peiyang Kela Hotel on the Peiyang Park Campus of Tianjin University. |
|
View 2017 Origami Engineering Workshop Map in a larger map
|
|
|
Contact | Copyright © 2013-2018, All rights reserved. |
|
|